Tramp Oil Separator System
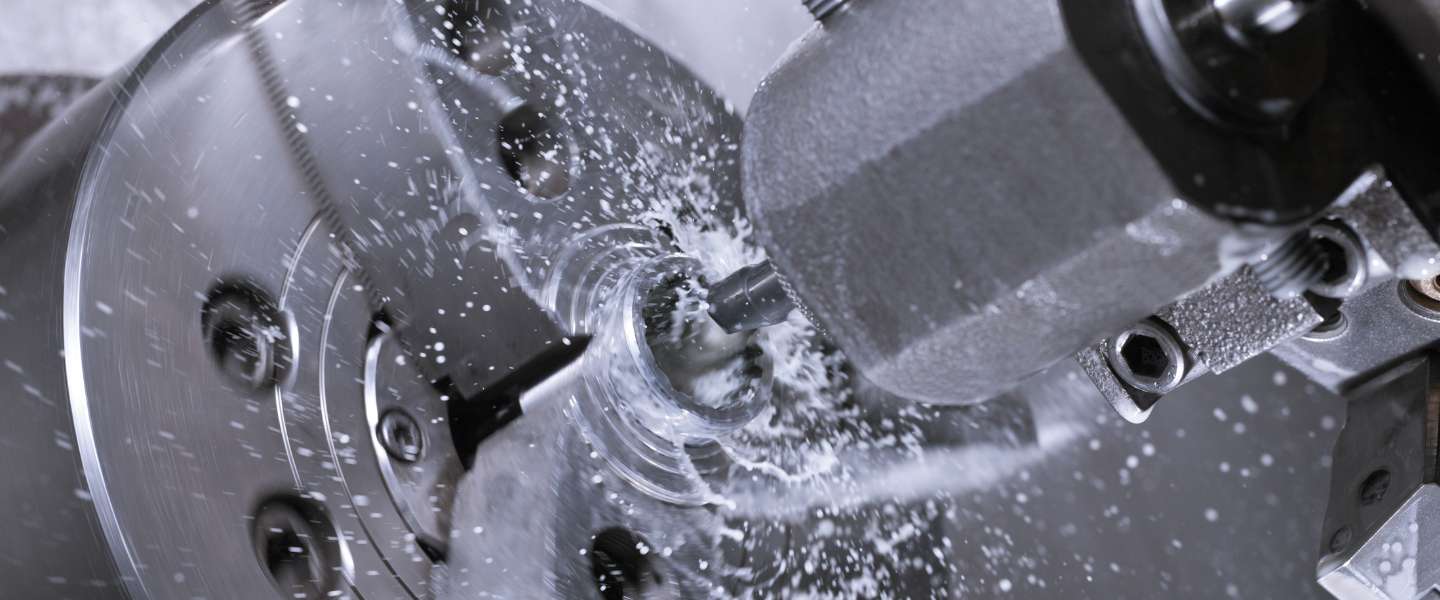
Toss Out Tramp Oil and Suspended Solids
Don’t let tramp oil and suspended solids in your machining fluids cause unnecessary downtime and repairs. Tackle the core issues of operational downtime and operational efficiency with our Tramp Oil Separation System (T.O.S.S.).
Our advanced solution removes tramp oil and suspended solids from water-based coolants, synthetic and semi-synthetic cutting fluids, and wash waste systems. T.O.S.S. efficiently removes free-floating, dispersed and loosely emulsified tramp oils. Its high-efficiency coalescing filter achieves oil separation to less than 0.5% by volume.
Simplify operations, cut fluid concentration purchases, reduce waste, and save money with this sustainable turnkey system.
T.O.S.S. Benefits By The Numbers
Less than ½%
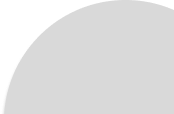
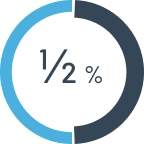
Filter Out Contaminants
T.O.S.S. offers a cost-effective solution for tramp oil issues. The self-contained system prolongs the lifespan of water-based coolants, synthetics, and alkaline wash water by eliminating free-floating, dispersed, and loosely emulsified tramp oils.
Features Include:
- Complete Solution. Compact system comprising a high-efficiency coalescing system, a large reservoir tank, and floating skimmers.
- Filtration Design Options. Three options for solids filtration: V-bottom design for heavy sludge, 100-micron bag filter for suspended solids, and an optional pre-filter for enhanced fluid cleanliness.
- Improved Filtration. Reduces tramp oil to less than ½% by volume.
- Efficient Oil Drainage. Eliminate water from free oil to achieve oil-water separation of 1-2%.
- Gravity Flow. Conserve energy by separating fluids naturally through gravity outlets.
- Rugged Construction. Industrial-grade steel construction with a chemical-resistant coating.
- Small Footprint. Self-contained, compact, skid-mounted unit takes up minimal floor space.
- Plug-and-Play Setup. Install without altering current processes for a smooth transition and rapid deployment.
24 Hours A Day
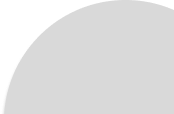

Reduce Coolant Costs
The T.O.S.S. Tramp Oil Separator is designed for various industrial environments, such as machine shops and manufacturing facilities, that need to remove tramp oils and suspended solids from their coolants and wash waters.
The tramp oil removal process uses coalescing technology to enhance the longevity and performance of machining fluids, driving cost savings and operational excellence.
The automated and self-contained design promotes sustainability by significantly reducing fluid purchases and hazardous waste.
Features Include:
- ≥ 99% uptime: Ensures continuous operation with minimal maintenance downtime.
- Clean Coolant: Provides clean coolant 24 hours a day to the shop floor.
- Waste Reduction: Achieves superior oil-water separation, draining free oil with minimal water content (1-2%).
- Lower Labor Costs: Automated oil discharge minimizes manual intervention, freeing up valuable labor resources.
- Ease of Use: Simple, plug-and-play setup and operation make it easy to integrate and train personnel.
- Safeguard Safety: Enhances safety and regulatory compliance by maintaining a cleaner working environment.
- Volume: Versatile filtration capabilities for various machining processes, with adjustable flow rates up to 50 GPM.
- Customizable: Modular design allows customization to accommodate specific industrial needs and flow rates.
Up to 80%
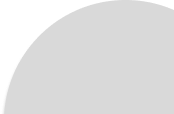
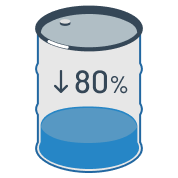
Reduce Coolant Costs
T.O.S.S. is ideal for metal working facilities with grinding, turning, general machining, and parts washing equipment that demand tramp oil removal.
The advanced filtration system aids optimal coolant sumps operation and also can be used as pre-treatment for chemical waste systems and fine filtration systems like micro, ultra, nano, or reverse osmosis systems.
Features Include:
- Lower Fluid Use. Reduce fluid purchases by up to 80% by enhancing fluid longevity.
- Coalescing System. Advanced coalescing technology removes visible and microscopic oil droplets and suspended solids from coolants and wash waters.
- Better Purification. Separate all forms of tramp oil, including mechanically dispersed oils mixed in from agitation.
- Safeguard Safety. Keep the working environment cleaner to improve safety and regulatory compliance.
- Cost Savings. Save on coolant replacement and maintenance with self-cleaning features and robust construction.
9 to 12 Months
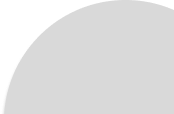
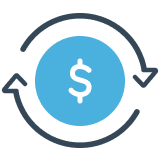
Rapid ROI
An investment in T.O.S.S. pays for itself in nine to 12 months. Operational expenses are reduced as the system cuts down on fluid purchases and disposal costs, improves machine performance, and ensures compliance with environmental standards.
Features Include:
- Operational Excellence. Extend the life of machine tools and coolants and trim maintenance downtime.
- Cost Efficient. Cut waste disposal costs by up to 90% and trim new fluid purchases by up to 85%.
- Environmental Compliance. Shrink the shop’s environmental footprint and improve compliance with environmental regulations.
- Better Workplace Safety. Combat hazardous fluid exposure with a cleaner workplace.
2 - 50 Gallons
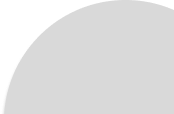
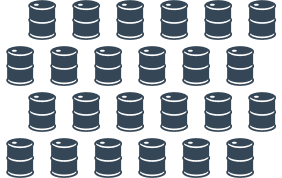
Improve Operational Efficiency
The T.O.S.S. Tramp Oil Separator uses advanced coalescing technology to remove tramp oil and suspended solids from coolants and wash waters, enhancing the longevity and performance of industrial fluids.
- Skimming the Surface
The EdjeTech floating skimmer, placed in the fluid reservoir, adjusts to the fluid surface, skimming off free-floating oils and capturing fluid with dispersed oil and suspended solids. - Filtering the Fluid
The skimmed fluid is drawn through the skimmer into a separator supply pump and then into a bag filter, where suspended solids are efficiently filtered out, leaving cleaner fluid. - Coalescing Media
The filtered fluid moves into the coalescing media with 132 square feet of surface area per cubic foot. Here, 99% of 20-micron oil droplets are separated on the first pass. - Returning Clean Fluid
The clarified fluid flows into a clean fluid chamber and is gently discharged back into the original reservoir through an adjustable overflow weir. - Automatic Oil Removal
Free oils rise to the tank's top, flow into the tramp oil discharge trough, and are automatically drained into a client-provided container, maintaining system efficiency without manual intervention.
Reduce by 90%
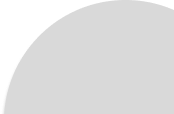
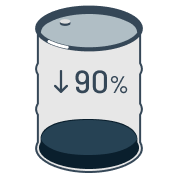
Slash Waste Disposal Costs
T.O.S.S. is suited for shops looking to upgrade their sustainability profile by reducing waste and associated disposal costs.
Features Include:
- Sustainable. Reclaim and recycle valuable oils for internal use or sale.
- Resale. Sell or reuse separated fluids to promote sustainable practices.
- Save Money. Lower new fluid purchases and hazardous waste disposal costs.
Fully Customizable
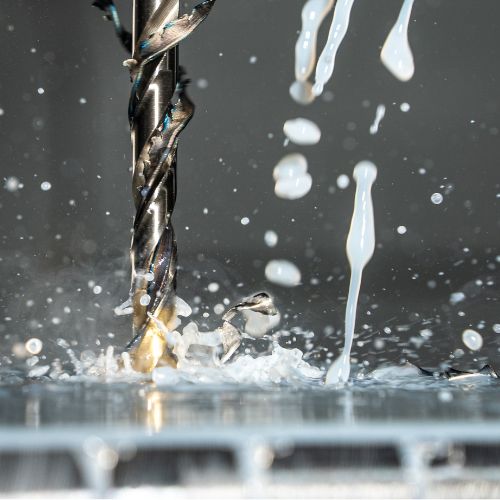
T.O.S.S. can be customized to fit specific flow rates, volumes, and space constraints for a variety of industrial applications. Choose from standard or custom sizes, add an air/electric pump, or opt for a portable unit to achieve optimal results in specific applications.
Fixed or Portable
Choose a fixed unit or opt for a portable one that can be moved to multiple machines.
Flexible Power Source
Air or electric separator supply pumps are available.
Skimmer Options
Install a vertical skimmer for shallow reservoirs or opt for a ballast skimmer for deep/large reservoirs.
Ozone Generator
Add an Ozone Generator to keep bacteria under control, odors at bay and improved workspace safety for personnel.
Flexible Flow Rates
To cater to filtration needs of varying volumes, flow rates range from 1 GPM to over 50 GPM.
Model | Flow Rate (GPM) | Max. Operating Temp. | Operating Capacity (US GAL.) | A (in) | B (in) | C (in) | D (in) |
---|---|---|---|---|---|---|---|
MT2 | 2 | 180°F | 25 | 33 | 12-1/4 | 42 | 24 |
MT3 | 3 | 180°F | 30 | 39 | 12-1/4 | 42 | 24 |
05 | 5 | 180°F | 37 | 48 | 12-1/4 | 42 | 24 |
10 | 10 | 180°F | 75 | 48 | 24-1/4 | 42 | 24 |
15 | 15 | 180°F | 110 | 48 | 36-1/4 | 42 | 24 |
25 | 25 | 180°F | 290 | 60 | 48-1/4 | 42 | 24 |
50 | 50 | 180°F | 400 | 72 | 36 | 66 | 24 |
Custom specifications available upon request. Contact us for more information. |