Tube Mill Coolant Recycling System
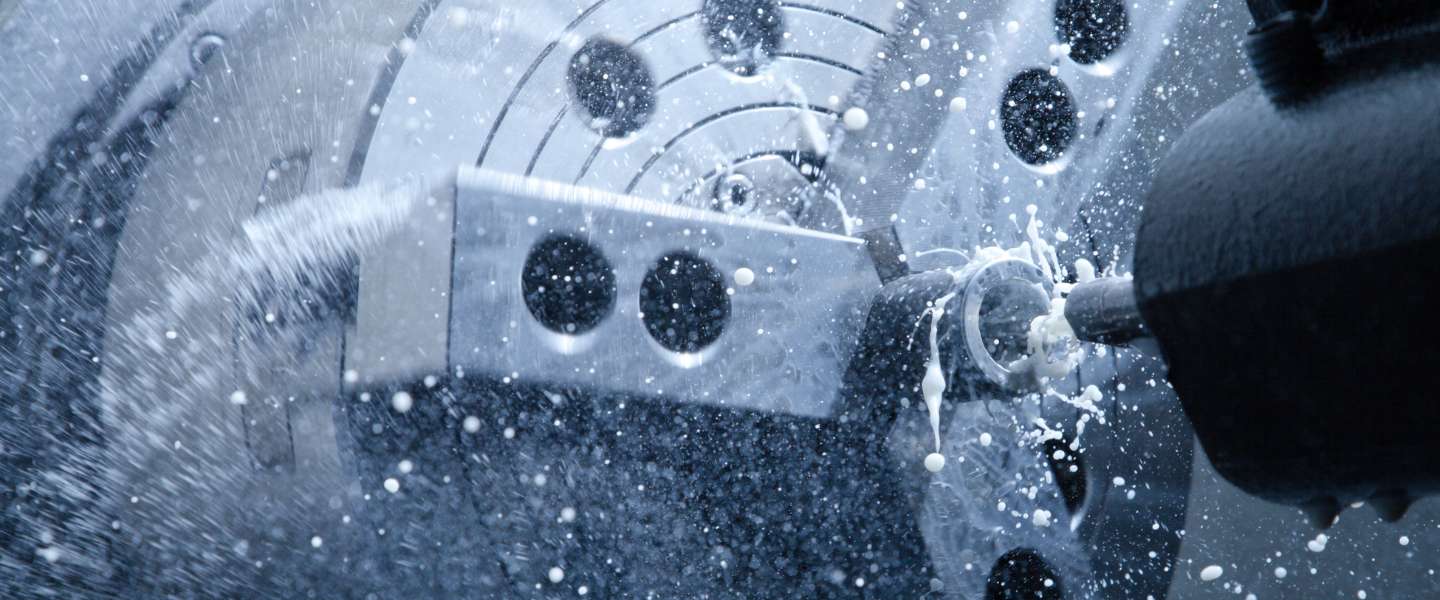
Extract Tramp Oil From Tube Mills for Faster, Cleaner Operations
Optimize your coolant lifecycle while maintaining operational efficiency with our specialized Tube Mill Coolant Recycling System (T.M.C.R.S.)
Our top-tier industrial coolant management system filters ferrous and non-ferrous materials and tube oils from coolant that can contaminate tube production and damage rolls.
This self-contained system extracts tramp oil and particulates automatically to extend coolant life, eliminate fluid bacteria, reduce mill pit clear outs, and keep fluid lines open.
Simplify operations, cut fluid concentration purchases, trim labor costs, slash mill downtime and save money with this eco-friendly turnkey system.
T.M.C.R.S. Benefits By The Numbers
99.75%
T.M.C.R.S. removes 99.75% of ferrous, non-ferrous particulates and tramp oil by volume. Extracted tramp oils has 2% or less water content.
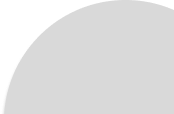
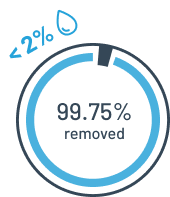
24 Hours A Day
T.M.C.R.S. provides operations with clean coolant 24 hours a day and ≥ 99% uptime.
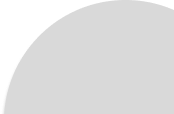

45% - 85%
T.M.C.R.S. reduces fluid purchases by up to 85%.
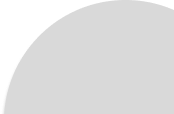
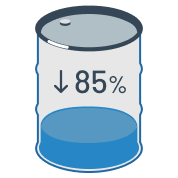
3 to 12 months
On average, our clients experience a payback period of 3 to 12 months, depending on fluid volumes.
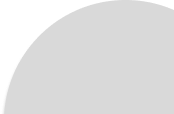
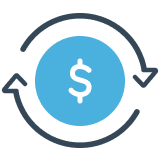
1600 GPM
T.M.C.R.S. can be customized for any volume, handling up to 990 GPM and scalable to 1,600 GPM or more.
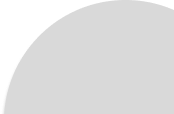
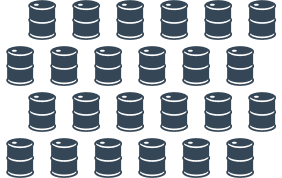
85% - 90%
T.M.C.R.S. cuts waste disposal costs by up to 90%.
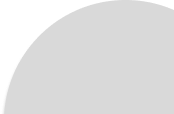
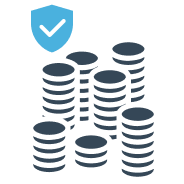
Fully Customizable
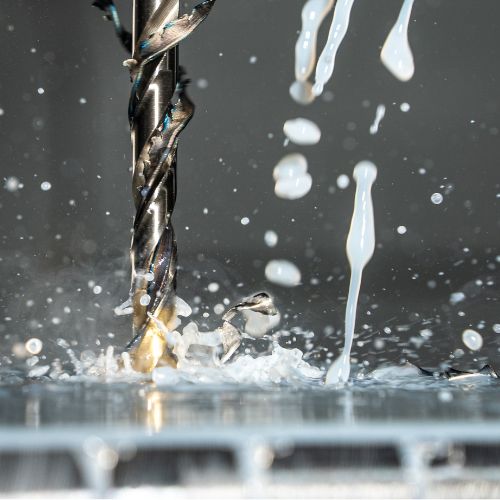